Heavy duty linear bearings play a crucial role in industrial automation, CNC machines, rail systems, and other high-load applications. They provide smooth, precise, and efficient linear motion, but like any mechanical component, they can experience issues over time. Understanding the common heavy duty linear bearings failures and their solutions can help prevent downtime, improve performance, and extend their lifespan. This article explores frequent problems encountered with heavy duty linear bearings and provides practical solutions to address them.
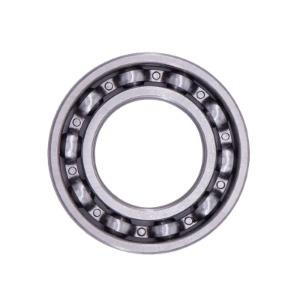
10-600 MM Corrosion Resistance Deep Groove Ball Bearing
1. Excessive Noise and Vibration
Causes:
Lack of lubrication or use of inappropriate lubricant.
Misalignment between the bearing and the guide rail.
Contamination from dust, debris, or metal shavings.
Overloading beyond the bearing's rated capacity.
Solutions:
Regularly lubricate the heavy duty linear bearings with the recommended grease or oil to ensure smooth motion.
Check and correct misalignment by properly mounting the bearing and guide rail.
Use protective seals or covers to prevent debris from entering the bearing system.
Ensure the bearing is not subjected to loads exceeding its design limits.
2. Premature Wear and Surface Damage
Causes:
Insufficient or irregular lubrication, causing to increased friction.
High operating speeds combined with high loads.
Poor-quality bearing materials or improper heat treatment.
Contaminants causing abrasive wear.
Solutions:
Implement a regular maintenance schedule to reapply lubrication and check for signs of wear.
Use heavy duty linear bearings made from high-quality, hardened steel or coated surfaces to withstand heavy loads.
Reduce excessive speeds and ensure proper load distribution.
Keep the working environment clean and use dust-proof covers if necessary.
3. Stick-Slip Motion (Irregular Movement)
Causes:
Uneven lubrication distribution causing inconsistent movement.
Corrosion or rust buildup on the guide rail or bearing components.
Improper preloading of the bearing, causing to excessive friction.
Solutions:
Apply uniform lubrication across the full length of the guide rail.
Use corrosion-resistant heavy duty linear bearings or apply anti-corrosion coatings to prevent rust formation.
Adjust preload settings carefully to balance stability and friction reduction.
4. Bearing Blockage or Seizure
Causes:
Foreign particles such as dirt, chips, or dust causing internal blockage.
Insufficient lubrication, causing to increased friction and overheating.
Overloading beyond the designed capacity, causing deformation or jamming.
Solutions:
Regularly clean heavy duty linear bearings and guide rails to prevent contamination.
Use appropriate lubrication and monitor temperature levels during operation.
Select a bearing with the appropriate load capacity and consider upgrading to a higher-rated model if overloading persists.
5. Loose Fit or Bearing Misalignment
Causes:
Poor installation causing to incorrect alignment with the rail.
Wear and tear over time, causing a loose fit between the bearing and rail.
Thermal expansion affecting metal components in varying temperature conditions.
Solutions:
Ensure proper installation procedures with precise alignment tools.
Replace worn-out bearings before they cause mechanical failures.
Consider temperature-resistant materials for environments with heat fluctuations.
6. Corrosion and Rust Formation
Causes:
Exposure to moisture, chemicals, or humidity.
Use of non-rust-resistant materials in harsh conditions.
Lack of proper protective coatings or lubrication.
Solutions:
Choose stainless steel heavy duty linear bearings or those with anti-corrosion coatings.
Apply rust-inhibiting lubricants and store bearings in dry, controlled environments.
Implement regular maintenance checks to detect and prevent rust buildup early.
Understanding and addressing common failures in heavy duty linear bearings can significantly improve operational efficiency and reduce unexpected downtime. Proper lubrication, alignment, and contamination prevention are key factors in maintaining their longevity. By following these solutions, industries relying on heavy duty linear bearings can enhance machine performance, reduce repair costs, and ensure smooth, consistent motion in high-load applications. Regular inspections and preventive maintenance are essential to keeping heavy duty linear bearings in working condition.