Ball bearings and taper roller bearings are essential components in numerous industrial and mechanical applications. These bearings are known for their unique attributes, which enhance their performance based on specific operational needs. In this article, we'll examine how ball bearings and taper roller bearings meet high-performance requirements, focusing on the significance of precision grades and structural designs.
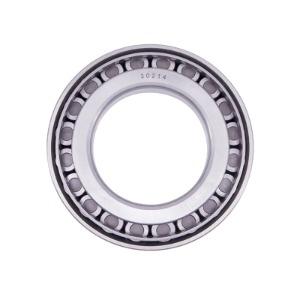
30306 30304 30204 Wheel High Precision Tapered Roller Bearing
The Role of Precision Grades in Ball Bearings
One of the primary factors influencing the performance of ball bearings is their precision grade. Precision is generally rated by the ABEC scale (Annular Bearing Engineering Committee), which measures factors such as dimensional and shape tolerances. Higher ABEC ratings correspond to tighter tolerances, allowing for increased rotational accuracy and smoother operation, which is critical for applications where even minimal vibrations or misalignments could impact performance.
Ball bearings with high ABEC ratings, such as ABEC-7 or ABEC-9, are widely used in high-speed applications like aerospace and precision machinery, where smooth rotation and minimal friction are essential. For example, the dimensional tolerance in these high-grade bearings is meticulously controlled to prevent any deviations in size or shape, ensuring consistent contact between balls and races. Such precision allows ball bearings to operate effectively under high-speed conditions without compromising stability or accuracy.
Structural Considerations: Size, Shape, and Tolerances
The precision of ball bearings also depends on factors like size and shape tolerances. Tighter tolerances in ball bearings contribute to better load distribution, reducing wear and extending the bearing's lifespan. Shape tolerance ensures that the ball and raceway surfaces maintain uniform contact during rotation, minimizing friction and heat buildup. Bearings used in demanding applications are often crafted from materials that can resist deformation and stress, preserving accuracy even under high loads.
The importance of precision becomes more apparent when considering applications in electronics, medical equipment, or automotive components.
Load Distribution and Durability in Taper Roller Bearings
Unlike ball bearings, which excel in managing radial loads, taper roller bearings are specifically designed to handle both radial and axial loads due to the unique shape and orientation of their rollers. The tapered design allows these bearings to distribute loads more evenly across the bearing surfaces. This characteristic makes taper roller bearings ideal for applications that involve significant axial forces, such as vehicle wheels or industrial machinery.
The angle of the rollers in taper roller bearings is a crucial factor affecting their load-bearing capacity. A steeper angle allows the bearing to handle larger axial loads, while a shallower angle focuses on balancing both radial and axial loads. For example, heavy machinery and automotive transmissions often use taper roller bearings with steeper angles to support greater axial loads without sacrificing performance.
In terms of durability, taper roller bearings are often made from robust materials, including steel alloys, which enhance their ability to withstand heavy loads and prolonged operation. These bearings can endure high-pressure environments, distributing forces effectively to maintain stability and reliability under continuous usage.
Sealing Structure for Contaminant Protection and Lubrication
One of the key features of taper roller bearings is the option of a sealing structure, which provides added protection against contaminants. In dusty or dirty environments, a well-designed seal can prevent harmful particles from entering the bearing, preserving the integrity of the rollers and races. Contaminants such as dust, dirt, or moisture can degrade the surfaces of bearings, increasing friction and reducing lifespan.
Sealed taper roller bearings also reduce the risk of lubrication loss, which is essential for smooth and reliable operation. Proper lubrication minimizes friction between rollers and raceways, preventing excessive heat generation that can damage the bearing over time. By maintaining adequate lubrication levels, the bearing's efficiency and durability are further enhanced, especially in heavy-duty industrial applications where equipment operates under constant stress.
Practical Applications and Performance Benefits
The precision and structural attributes of ball bearings and taper roller bearings make them indispensable across various industries. In precision machinery, ball bearings with high ABEC grades provide the rotational accuracy needed for intricate operations, while taper roller bearings offer durability in load-intensive scenarios like construction machinery or vehicle drivetrains.
In addition, both types of bearings are designed to improve performance efficiency, whether by reducing friction, balancing loads, or preventing contaminant ingress. By understanding the distinct features and applications of ball and taper roller bearings, engineers and technicians can select the right type of bearing to match specific operational needs, ultimately enhancing both equipment performance and longevity.