In the ever-evolving world of manufacturing, efficiency and precision are paramount. Small bearings and deep groove ball bearings are two essential components that contribute significantly to this goal. Each has unique characteristics that make them suitable for specific applications, and when used together, they can optimize performance and durability in various industrial settings.
The Role of Small Bearings and Deep Groove Ball Bearings in Manufacturing
Small bearings and deep groove ball bearings hold a vital place in manufacturing. Small bearings are typically compact and lightweight, making them good for precision machinery where space is limited. Deep groove ball bearings, on the other hand, are known for their robustness and ability to handle radial and axial loads. Their durability and versatility allow them to be used in various applications, from automotive to industrial machinery. Together, these two types of bearings address the need for components that can handle both high speeds and precision without compromising on durability.
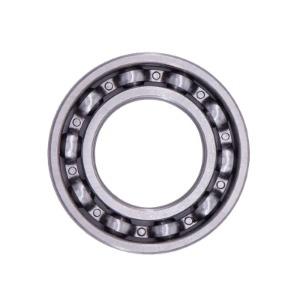
10-600 MM Corrosion Resistance Deep Groove Ball Bearing
Technical Comparison: Differences and Similarities
To understand the synergy between small bearings and deep groove ball bearings, it's essential to compare their technical aspects.
Size and Structure: Small bearings are generally compact, designed for applications where size constraints are a concern. In contrast, deep groove ball bearings come in a wider range of sizes, making them more adaptable to different load requirements. They have a simple structure, with deep grooves in the inner and outer rings that enhance load-bearing capacity.
Performance and Load Capacity: Small bearings excel in high-speed, low-load environments, commonly found in small appliances, precision equipment, and electronics. Deep groove ball bearings, however, are designed to handle both radial and axial loads efficiently, making them ideal for heavy-duty machinery that requires both stability and endurance.
Applications: Small bearings are commonly used in sectors like robotics, medical devices, and micro-machinery due to their precise motion control. Meanwhile, deep groove ball bearings find applications in more extensive systems, such as automotive transmissions, industrial fans, and conveyors, where they provide stability under varying loads.
Real-World Applications: When Small Bearings and Deep Groove Ball Bearings Join Forces
In real-world manufacturing, small bearings and deep groove ball bearings often work hand-in-hand to enhance efficiency and performance. For instance, in the assembly of conveyor systems, deep groove ball bearings provide the necessary support for handling large, heavy loads along the conveyor line. At the same time, small bearings are integrated into the motorized components to control motion and maintain precision. This collaboration allows the system to operate smoothly and efficiently, handling both large-scale movements and intricate adjustments.
In precision machinery like CNC machines, small bearings offer the fine motion control required for intricate tasks, while deep groove ball bearings maintain the machine's overall stability, absorbing vibrations and ensuring smooth operation at high speeds. This combination not only extends the lifespan of the equipment but also ensures the accuracy and reliability of the machine's output.
Market Trends: Rising Demand in the Manufacturing Sector
The demand for small bearings and deep groove ball bearings is on the rise in the manufacturing industry. As automation and precision technology continue to advance, the need for reliable, high-performance components grows. Companies are increasingly seeking bearings that can withstand high speeds, operate in compact spaces, and deliver accurate motion control. In particular, deep groove ball bearings are expected to see a steady rise in demand due to their durability and wide range of applications.
Furthermore, the push towards smaller, more efficient machinery in industries like electronics and medical equipment is driving up the need for small bearings. These components allow for the creation of lightweight, compact devices without sacrificing performance.
Practical Tips for Choosing the Right Bearings
Selecting the right bearing type can significantly impact machinery performance and longevity. Here are some practical tips to guide your decision:
Consider the Application: For precision instruments or applications with space limitations, small bearings are ideal. On the other hand, if the application involves significant radial or axial loads, deep groove ball bearings will provide the necessary support.
Evaluate Performance Needs: Look at the operating speed, load capacity, and environmental conditions. Small bearings are better suited for high-speed, low-load applications, while deep groove ball bearings excel in heavy-duty and high-load settings.
Brand and Quality: Opt for reputable brands that guarantee quality and durability. Poor-quality bearings can casue to frequent maintenance, reducing overall productivity and increasing costs.
Cost vs. Longevity: While high-quality bearings might be more expensive upfront, their longevity and reliability often make them more cost-effective in the long run.
Consult Experts: If unsure, consult a supplier or industry expert. They can provide insights into the options based on your specific needs, ensuring you choose bearings that meet your performance requirements.